Cyber-physical lab project part of DARPA Advanced Vehicle Make program

A half dozen undergraduates gathered in the Featheringill Hall cyber-physical lab on a Wednesday afternoon to figure out ways to make a radio-controlled car do some pretty cool stuff. Students manipulated computer-aided design models on multiple screens near a table strewn with car parts and molded plastic models. What seemed like child’s play was so much more.
The lab’s work is an outgrowth of a huge DARPA (Defense Advanced Research Projects Agency) project, of which Vanderbilt is a major participant, designed to revolutionize the way the Pentagon supplies vehicles for the nation’s troops. The idea is to churn out those vehicles faster and cheaper, with digital designs, rapid manufacturing, software innovation and social collaboration around open-source vehicle design (see FANG design challenges).
The cyber-physical lab was established with seed money from Vanderbilt. The lab explores and tests ideas for the design process of the larger project, called Adaptive Vehicle Make (AVM) program.
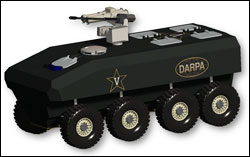
Last summer, four undergraduate students collaborated on the initial cyber physical modeling of an armored personnel carrier while the work continued during the 2011-2012 school year with 15 more students at work on a 1:5 scale electromechanical vehicle. The project involved 20 more students for paid internships this past summer.
“What we’ve done is create an industrial setting in the shell of an academic setting so the students are getting real-world experience. This is the true cross-pollination of inter-disciplinary research,” said Ryan Wrenn, a research engineer with Vanderbilt’s Institute for Software Integrated Systems (ISIS), who works with the undergraduates in the lab.
The students immerse themselves in solving complex problems that ultimately will make the vehicle’s design easy to test and easy to change according to rapidly evolving needs, terrains and conditions.
The goal is to develop programs to test the designs before they are built, said ISIS staff engineer James Klingler. “You build a computer model first and then fine-tune the components and software,” he explained.

Phil Ingram, a mechanical engineering senior from Denver, Colo., found out about the cy-phy lab work from Tom Withrow and jumped at the chance to spend more time with computer modeling. Withrow, assistant professor of the practice of mechanical engineering, provides the faculty link between ISIS and the undergraduate lab.
“We’re actually learning a subset of skills that we can apply to future jobs,” Ingram said. In fact, Ingram has a job lined up following graduation with OSIsoft, headquartered in San Leandro, Calif.
Jason Lee, a junior mechanical engineering major from Westchester, NY, finds the lab creative and flexible with work that parallels his academic courses. Originally leaning toward a finance degree, the computer-aided design (CAD) work, while tedious and meticulous at times, convinced him that an engineering career would be more interesting to him.
“This is not what I expected to be doing, but I’m glad I found it,” Lee said.
Using system-based architecture, the students are challenged to come up with truly novel designs that can be fabricated quickly.
The first full-featured prototype was a radio-controlled car a little bit larger than a microwave oven. The team used commercially available parts and open-source software solutions.
“The idea is to attain better performance with a vehicle that can adapt quickly to changing needs,” explained Withrow. “This kind of multi-systems engineering is the future of engineering.”
ISIS is a key site for design and testing of the AVM components and serves as “curator” of the component context and manufacturing library. AVM, a flagship initiative of DARPA, represents a challenge to a large research team that includes representatives of prominent institutes, corporations and universities, including Vanderbilt. Industry partners for the project include Boeing, BAE systems and Ricardo. The idea, according to DARPA, is to eliminate “multiple iterations of the design-build-test-redesign cycle.”
The AVM portfolio consists of three primary programs: META, software design verification and validation, which is largely centered at ISIS; Instant Foundry Adaptive through Bits (iFAB); and Fast Adaptable Next-Generation Ground Vehicle (FANG). The FANG program includes a prize challenge and a crowd-sourced manufacturing outreach effort.
The undergraduate lab meets a mentoring component designed to motivate a new generation of manufacturing and design innovators. According to Withrow, there are plans to transition the undergraduate lab work into a course on electro-mechanical vehicle design.
“It’s very meaningful for the overall objective of the project to include participation by undergraduates,” he said. But more than that, the undergraduates are key players to this work. “This lab is important in two main purposes. First, it demonstrated that the work we’re doing with AVM is viable and, second, perhaps more importantly, it helps us train our next generation of engineers.”
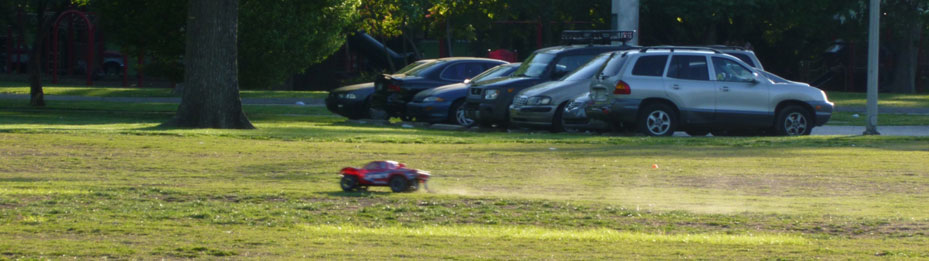