Mechanical engineering design students preparing for the NASA Student Launch competition May 17 recently ground tested their microgravity liquid fuel tank design in preparation for the 2014 national event in Utah.
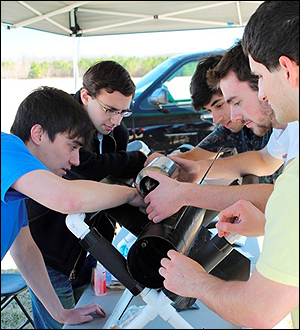
“Among the various projects suggested by the NASA program was the ‘liquid sloshing research in microgravity’ to support liquid propulsion system upgrades and development. The Vanderbilt Aerospace Club project incorporates this requirement into a much more major undertaking by designing a bio-fuel delivery system to ignite a high bypass ramjet engine during rocket flight,” said Amrutur V. Anilkumar, club director and professor of the practice of mechanical engineering.
The NASA Student Launch is a research-based university competition that provides relevant and cost-effective research and development support for the Space Launch System (SLS). Supported by the NASA Human Operations Mission Directorate and the US Aerospace Industry, it is an engineering design challenge where the research projects are conceived by NASA and the industry partners.
“Atmospheric rocket flight offers unique challenges for handling liquids. First, there is the issue of liquid slosh due to vibration during the rocket motor burn phase. Next, and more importantly, there is the issue of rapid deceleration touching -2.7 gravitational force (-g is downward acceleration) following rocket main engine cut off due to atmospheric drag and free fall.
Flipping a fuel tank
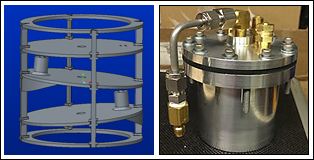
“The result of this is that the liquid instantaneously hits the roof; -2.7 g deceleration is much worse than the microgravity slosh conditions for which fuel containers have to be designed for space flight,” Anilkumar said.
“Through a series of two rocket flights and a very ingenious mechanism for bubble trapping, the team has designed a fuel tank than can operate upside down, and can handle lateral and axial vibrations,” Anilkumar added.
“The main requirement is that our design should be able to deliver fuel on demand for any orbital engine firing in Space. Liquid in zero gravity can reside anywhere in a tank, and especially vexing is the reality that it would not be close to the pickup,” said team member Shivaprem Bernath.
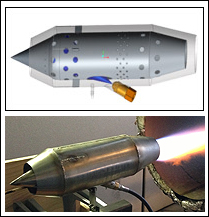
“Space fuel tanks are designed to be of the liquid baffle type where fuel is literally squeezed out. We did not want to follow that approach, as it would require too many moving parts and the liquid would not be reliably deliverable in a few seconds of rocket flight,” said Patrick Foran, fuel delivery system design leader.
In their rocket flight, the team plans to ignite an externally mounted ramjet engine, four seconds into rocket launch, just following main engine cutoff.
“At this stage of rapid deceleration, we need to be delivering 10cc/s (cubic centimeters) of fuel for 10 seconds of engine testing, with no interruptions or bubbles,” said Kevin Bush, who led the team effort on the design and fabrication of the ramjet engine.
Elaborate design
“Our ramjet design came out of the design playbook of old fashioned physical reasoning, back-of-the envelope calculations, and advanced computational fluid dynamic simulations,” said Jordan Salik, the CFD expert on the team.
“Imagine the scenario when the liquid hits the roof, all we are left with is air at the fuel pickup. Air in the line will extinguish the engine instantaneously and if we can solve this problem, we can solve the Space Fluid Management problem,” said Chris Twedell, a team member on the design team.
- Dr. Mark Whorton (left), director, Systems Development & Operations, Teledyne Brown Engineering, and Patrick Foran.
Fuel tank design places in AIAA’s student competition
Patrick Foran recently presented the fuel tank innovation in the undergraduate student research competition at the American Institute of Aeronautics and Astronautics’ Region II Conference in Memphis April 7-9, and captured second prize in a field of 16 competing universities. Topics ranged from satellite cluster formation using differential drag to testing and evaluation of hybrid rocket engines. Shiva Bernath, who also attended the conference, said, “Industry professionals were amazed at the amount of hands-on work that had gone into fabricating this novel fuel delivery system, and they were especially appreciative of our no-frills demonstration.”
“We have set up an elaborate multilayer trap for the air, with small through-flow bobbins to only allow fuel to keep moving towards the pick-up, regardless of the tank orientation. Fuel just drains down as if it is being squeezed out, though we are operating with a rigid container,” Foran said.
“Recently, we ground tested the fuel tank performance at 450 psi manifold delivery pressure with the tank upside down and were able to extract fuel all the way to the fuel pickup; the fuel saw no change in orientation,” added Foran.
“We have a very robust ground-based testing protocol where we put our systems through rigorous testing; flight is the final ratification of our designs,” said Brandon Dimmig, president of the Aerospace Club.
“A passive fuel management and slosh abatement system as designed can have applications in the design of small satellites and space vehicles, where one can avoid the complexity of moving parts and the associated reliability and failure issues,” according to Professor Anilkumar.
Among the team members, Patrick Foran is looking forward to a design career at either Space-X or at Mercedes Benz. Chris Twedell will be joining Lockheed Martin as a Launch Engineer. Brandon Dimmig will work for the nuclear aircraft carrier manufacturer Huntington Ingalls as an instrumentation engineer, and Kevin Bush is heading to Stanford University to do graduate studies in energy engineering.
The activities of the aerospace club are sponsored by the Tennessee Space Grant Consortium and the Department of Mechanical Engineering.