Every month or so an article comes out reporting that some new object has been made using 3D printing: Everything from jewelry to prosthetic devices to electronic circuit boards to assault rifles to automobiles has now been created in this fashion. The prospect that this revolutionary manufacturing method will have a major impact on how we construct the various concrete structures that dominate the modern built environment brought almost three dozen experts to the Vanderbilt University campus July 16-17 to identify the areas of research required to realize its full potential.
“Clearly this is an emerging technology,” said Florence Sanchez, associate professor of civil and environmental engineering at Vanderbilt, who organized the meeting along with Jan Olek at Purdue University and Joseph Biernacki at Tennessee Technological University. “The goal of this workshop is to explore how this new technology can help us to develop innovative new infrastructure materials.”
For decades, the construction industry has been using the hydraulic, Portland cement model of construction. Cement is mixed with sand. Water is added to produce a slurry. The slurry is poured into wooden and metal forms where it sets up and the forms are removed.
The problems with this method are that it is slow, labor-intensive, and, as a result, expensive. “We’ve actually made tremendous progress in recent years coming up with new types of concrete with improved properties,” said Henri Van Damme of the Massachusetts Institute of Technology-French National Center for Scientific Research joint research unit, “but we are still stuck working with forms, which account for most of the labor and the cost.” 3D printing – formally called additive manufacturing – has the potential to replace the existing Portland cement technology. In fact, workshop members reported a number of “precursor” efforts at 3D printing with concrete:
- California architects Rael San Fratello created a 12-foot by 12-foot pavilion in a traditional Thai flower pattern made from 3D printed blocks. Last year they did a case study for a 3D printed house for a Beijing resort.
- Shanghai-based Win Sun Decoration Design Engineering Company has used 3D printing to construct a six-story apartment building out of recycled concrete material.
- Last year Minnesota contractor Andrew Rudenko completed a miniature cement castle made out of components produced by a 3D printer. It was a two-year project.
“Everyone is very excited about this,” said Sanchez. “It raises so many possibilities that no one can think of them all.” Architects are excited because the technology could allow them to make buildings in new shapes. Contractors are interested because it could allow them to build structures without external forms—by building up layers of material on an internal skeleton, for example.Civil engineers are intrigued because it may allow them to replace current cement-based mixtures with new materials that make the construction process faster, cheaper and more flexible.
Tracie Prater from NASA’s Marshall Space Flight Centerin Huntsville provided some insights into the potential advantages that this new process can confer. She reported that they have been experimenting with the use of 3D printing to make rocket engines and have found that they can make them from significantly fewer parts with significantly fewer welds at a potential cost savings from 40 percent to 75 percent. The rapid progress of 3D printing plastics and metals has been possible because the feedstocks (plastic and metal powders) are very uniform and their physical and chemical properties have been studied extensively.
Cement, however, is a much different material. “Cement is much more complex: If you change one ingredient then all the properties can change,” said Sanchez. Since it became a common building material in the 1800’s, knowledge of its behavior is based almost entirely on trial and error. As a result, the details of the chemistry and thermodynamics involved remain poorly known.
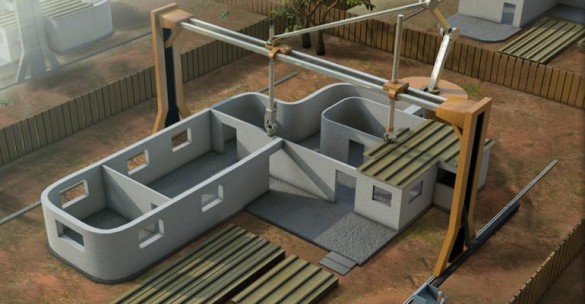
Artist conception of 3D printing system that can rapidly construct a residence. (Courtesy of Contour Craft / USC)
“I’ve worked on concrete issues for 26 years,” said Edward Garboczi of the National Institute of Standards and Technology. “During that time a number of things have come along … that I hoped would spur funding for research into the material’s basic properties but none of them panned out. 3D printing is a huge thing, so it may be different.” The complex nature and the variability of cement-based materials make them particularly difficult to adapt to 3D printing. That was demonstrated by an internally funded project in 2008 at Oak Ridge National Laboratory designed to demonstrate that 3D printing can be used to construct low-rise residential and commercial buildings for half the cost of conventional methods. It took a team of scientists and engineers two years of painstaking experimentation to come up the right combination of hardware and cement-based material to get the 3D printing process to work, reported ORNL’s Catherine Mattus. Since then, the U.S. Department of Energy has established a Manufacturing Demonstration Facility at ORNL to address the challenges related to advanced manufacturing technologies.
One particularly interesting approach for designing innovative new building materials discussed at the workshop is using 3D printing to imitate natural materials with extraordinary mechanical properties. One of the people pursuing this biomimetics approach is Pablo Zavattieri from Purdue who briefed the group on his efforts to understand several of these bioinorganic materials. One of them is nacre, or mother of pearl. It is the iridescent material in the outer layer of pearls and on the inside of many mollusk shells. It is formed from hexagonal platelets of the common mineral aragonite, arranged in thin layers separated by sheets of biological polymers. This configuration makes nacre a 1,000 times stronger than ordinary aragonite crystals. Zavattieri has used computer simulations and 3D printing to produce materials that duplicate its basic structure.
The product of the workshop, which was funded by National Science Foundation grant CMMI-1239979, will be a paper containing a series of recommendations on the specific areas of research that should be pursued to extend this revolution in manufacturing technology to the construction industry.
Contact:
David Salisbury, (615) 322-NEWS
david.salisbury@vanderbilt.edu