Orthopaedic surgeons typically look at X-ray or CT images of a broken arm bone and hold up an old-school ruler to confirm the best plate type and size for repair.
But the process is not always that easy, especially in cases involving complex fractures. And without years of experience to inform their estimates, young surgeons may need more time in the operating room to get a good fit.
A team of biomedical engineering seniors set out to show how a replica of the damaged bone would streamline the process, creating 3D printed humerus bones from prior cases at Vanderbilt University Medical Center. The humerus is among the longest bones in the human body, and arm fractures account for 50 percent of broken bones in adults.
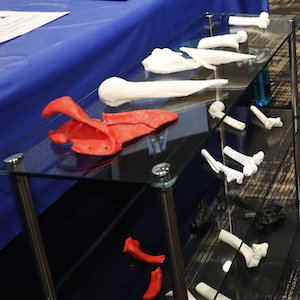
The team asked three surgeons to examine four pre-surgery versions of 10 humerus fractures: an X-ray, a two-dimensional CT scan, a 3D rendering and a 3D printed bone model. The retrospective study used complex distal humerus fractures that surgeons had repaired at VUMC.
Engineering students James Ford, Rachel Howell, Ivy Lee, Annalee Schuck and Caroline Stiles, all in the Class of 2018, analyzed the results and hope to co-publish a journal article on their findings. They presented their preliminary findings, methods, and a portfolio of 3D printed bones at Design Day in April.
For their two-semester senior design project the students worked with Dr. Donald Lee, professor of orthopaedic surgery and rehabilitation, and Dr. Sumit Pruthi, associate professor of radiology and radiological sciences and of pediatrics. Pruthi helped establish the new 3-D Printing Center at Monroe Carell Jr. Children’s Hospital at Vanderbilt, which serves both pediatric and adult cases.
“The purpose of the study was to determine if 3D printing of distal humerus fractures helps surgeons predict the appropriate operative approach and type of operative fixation of these fractures,” Lee said. “Distal humerus fractures were picked, since they were relatively common fractures, with complex anatomy.”
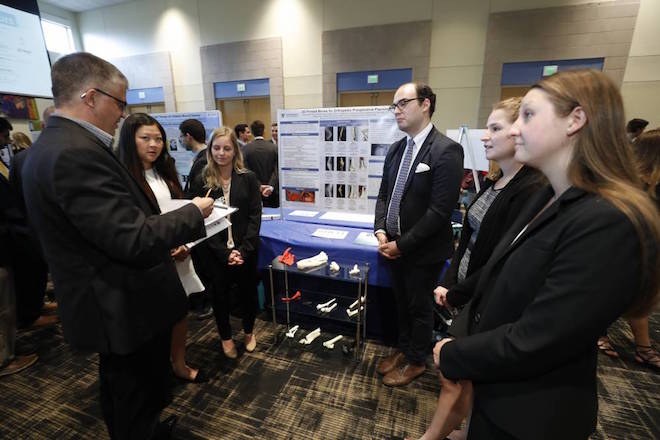
In a separate case, the group printed a complex scapula fracture before surgery.
“The surgeon was able to physically pick up the printed bone and move it around and fit the plates, even contouring them in advance before sterilizing it for surgery,” Howell said.
All of the student team members were attracted to a senior design project with direct patient impact. Ford, who plans to attend medical school, said a small amount of data can show clear differences, particularly in medial fractures.
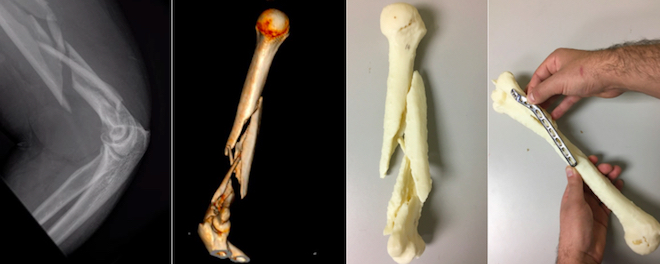
The 3-D Printing Center currently has three 3D printers that have the ability to create models that range in size from the width of a human hair to the length of a leg. A structured light-based 3D scanner is also part of the equipment, and all of the printers use Materialise Mimics Innovation Suite, the only FDA medically cleared 3D printing software.
“One of the goals at Vanderbilt is innovation, and this technology certainly is in keeping with that mission. 3D printing is innovative and part of the future of medicine,” Pruthi said. “The models can be used for patient education, medical student and resident education/training, surgical planning and simulation.”