
A failing pipe can be tough to spot. It may cause a puddle, produce another sign of damage, or simply burst before detection. A flooded kitchen or laundry room is messy and inconvenient, but the stakes are much, much higher in nuclear power plants – which on average contain many miles of pipeline.
As concern about aging plants escalates, Vanderbilt engineers are working on an early warning system. They are using polymer coatings on the inside of the pipe and 3D-printed polymer devices infused with nanoparticles as sensors to signal the changes on the outside of the pipe. And, they hope, sound.
A huge challenge is to detect the changes in the polymer film occurring inside the pipe. To create a useful and proactive technique, the team wants to use sound, or vibrometry, to identify these internal changes from outside the pipe.
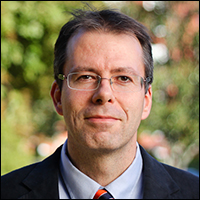
“We are designing and preparing coatings that can grab or chelate metal ions released from the corrosion process within a pipe,” said Kane Jennings, professor of chemical and biomolecular engineering.
“The films can chelate metal ions in solution and from a corroding surface. The chelated metals change the properties of the polymer films to effectively cross-link the polymer chains,” said Kane, who also chairs the department.
Early results are promising. Vibrometry does show slight changes when the metals are bound to the coating, Jennings said, and ongoing research is evaluating reliability at different coating thickness. The sensor for the outside of the pipe works – the coating changes from green to blue on a change in input that could signal the corrosion process.
“Ultimately the sensor would need to interface with the vibrometry to provide a stop/go color signal on the health inside of the pipe,” Jennings said.
An Electric Power Research Institute study that reviewed pipe safety at U.S nuclear power stations over a 36-year period found 1,816 pipe failures that were identified by testing and inspection. Another 2,247 failures were found after pipes had leaked, and in some cases, causing worker fatalities.
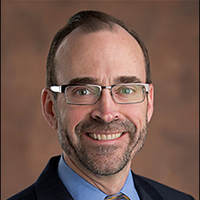
Pipelines in nuclear power plants transport “cooling” water, which is near boiling, to the reactor and to spent fuel pools. Pipes supply hydrogen gas to generators and transport steam to the main turbine, among many other functions. The idea would be to start by coating cooling pipe junctions and connections.
Research has involved faculty and graduate students in chemical, mechanical and civil engineering. Cole Brubaker, Ph.D. ’18, developed the sensors using metal-doped zinc sulfide phosphor materials. “3D-printed alternating current electroluminescent devices” was published in the Journal of Materials Chemistry in May 2019. Doug Adams, Daniel F. Flowers Professor and chair of the Department of Civil and Environmental Engineering, was the principal investigator. Jennings is the principal investigator on a paper that confirms the foundational chemistry published in September 2019 in the Journal of Physical Chemistry.
The work is supported by the Department of Energy’s Nuclear Energy Enabling Technologies program, grant DE-NE 0008712.
Contact:
Pamela Coyle (615) 343-5495
Pam.Coyle@Vanderbilt.edu
Twitter @VUEngineering