A novel redesign of industrial exhaust stacks by four mechanical engineering seniors that could result in 12% energy savings for their corporate sponsor has earned the student design team a second-place win in the team division at the American Institute of Aeronautics and Astronautics Region II conference last week.
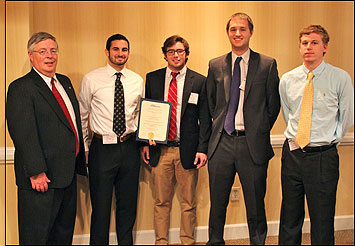
The students submitted a technical paper about their senior design project for the AIAA regional student chapter conference at North Carolina State University. The student conferences are a forum to present technical papers in competition.
The team will reveal their project April 19 in Featheringill Hall at Senior Design Day, 3-5 p.m. More than 60 projects by interdisciplinary teams will be on display.
Eric Citron, John Hamilton, Steven Jacobson and Karl Mecklenborg examined the exhaust stacks for continuously operating industrial furnace facilities with the intent to lower energy usage at Denso Manufacturing Tennessee, Inc. in Maryville, which is part of a global company that manufactures components, systems and advanced technology for all major automakers.
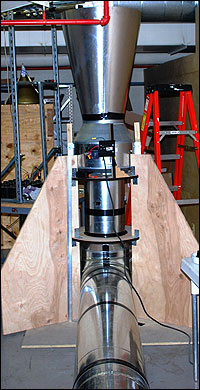
“We were a bit disappointed that we did not win the competition outright. The judges felt that our presentation was excellent, but we could have done a slightly better job on the paper,” Citron said.
Their design modification examines the benefit accruing from lowering the pressure load on the exhaust fans.
“These exhaust facilities use 15kW of power and run continuously 24 hours a day. Any energy savings would be a welcome improvement,” said Denso Director of Operations Britt Autry, a Vanderbilt mechanical engineering graduate (BE’92) who is at the forefront of optimizing energy use at Denso.
The team systematically designed a one-third scale model of the exhaust facility. Through detailed flow and energy measurements, they identified energy savings of about 12% in the redesign of the exhaust stack, which further increases to 15% in the presence of an energy recovery turbine.
“The most important finding in our study is that the exhaust fan produces a higher average volumetric flux (flow velocity) than does the baseline configuration, while consuming the same amount of power as a result of the lowered pressure load. This result holds strong implications for any industrial facility,” Citron said.
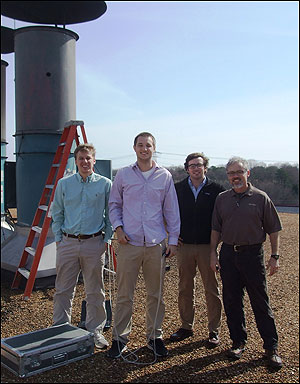
“We believe the costs involved in the modification can be easily recovered in fewer than four years,” said team leader Steven Jacobson.
“Their scale model studies have been complemented by visits to Denso where the students made on-site measurements of flow velocity profiles and energy consumption. Their approach to measurement and meticulous record keeping has been the hallmark of the engineering approach,” said Amrutur Anilkumar, mechanical engineering professor, project adviser and the students’ mentor.
“There are two design suggestions here,” said Anilkumar, “one is the optimal duct design and the other is the addition of an energy recovery turbine. “However, from a risk and reliability standpoint, the design of an optimal duct could be very appealing to a facility manager as there is no possibility for work stoppage.”