Rockets naturally roll during ascent, posing great difficulty in imaging objects on the ground. Engineering students in the Vanderbilt Aerospace Design Laboratory tackled that challenge. On Saturday, April 7, at the 2018 NASA Student Launch Competition in Toney, Alabama, they will demonstrate a payload design that helps capture image targets
The Vanderbilt team has designed a novel two-part rocket with sectional roll control (SRC) that enables the forward payload section to steadily image ground targets while the bottom section compensates for the rocket’s natural roll.

“Stabilizing the rocket payload section to take pictures of targets as the rocket is in rapid ascent at 400 mph, and naturally rolling about its axis, is a very complicated challenge that the team has solved, said Professor Amrutur Anilkumar, director of the VADL and team adviser. “Sectional roll control can come in handy in spacecraft design for targeting, mating and servicing of spacecraft in orbit.”
This year, 45 university and college teams are competing in the annual launch competition. Vanderbilt has been a four-time national champion of the NASA contest.
Twenty-one engineering seniors and graduate students are part of the VADL team competing in the NASA challenge. Robin Midgett, the VADL manager, is the team rocketry adviser. William Emfinger, adjunct assistant professor of mechanical engineering, is the software systems engineering advisor, and Ben Gasser, graduate student in mechanical engineering, is a rocket fabrication mentor.
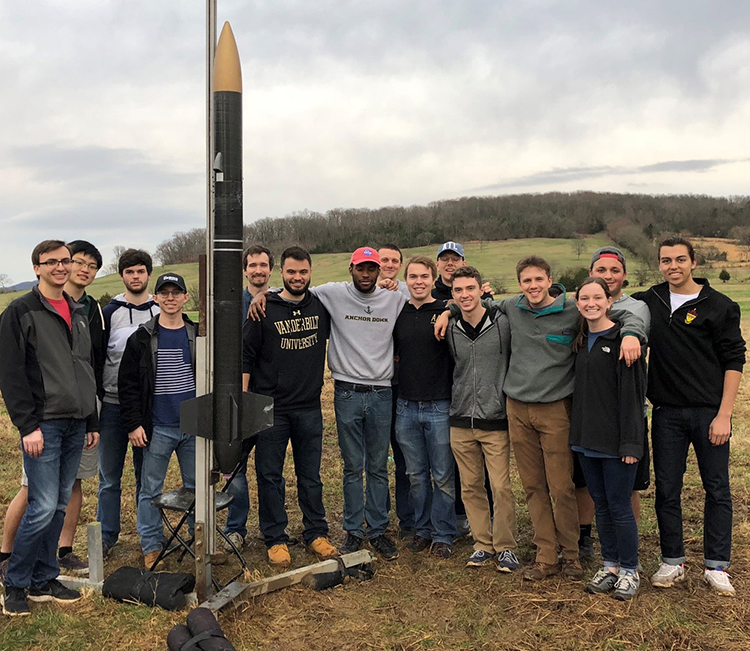
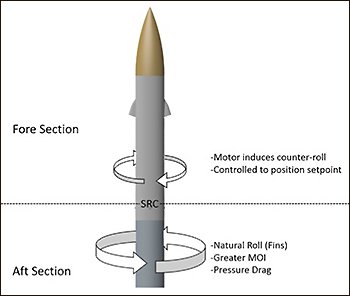
“Controlling the orientation of the payload section of the vehicle allows the imaging cameras to maintain the targets in the image frame. This is achieved by decoupling the fore and aft sections of the rocket and actuating the connection with a brushless DC motor,” said Dominic Ghilardi, the rocket design team leader.
“The payload incorporates two redundant cameras, each connected to a dedicated Image Processing Unit (IPU). The two parallel IPUs locate the ground-based targets in the frame of the image. An additional single-board computer takes inputs from the IPUs and an inertial measurement unit (IMU) to calculate the distance and heading from the vehicle to the targets,” said payload team leader Will Pagano.
Software integration across multiple devices is a significant element of payload complexity. The ROSMOD software suite, developed at Vanderbilt’s Institute for Software Integrated Systems, provides an effective platform for inter-device communication and real-time system response. Graphics processing units are leveraged on the IPUs to improve image processing latency and throughput to provide real-time performance.
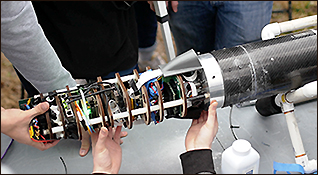
“The integration of hardware and software allows the novel SRC system to respond in real-time. This helps orient the vehicle’s payload section so that the ground-based targets remain in frame throughout the duration of the flight experiment,” said Jered Trujillo, the image processing engineer on the team.
The NASA Student Launch is a research-based, competitive project that provides cost-effective research and development to support the Space Launch System, or SLS. The SLS Program Office in collaboration with SLS industry partners determines research topics.
The competition involves an eight-month commitment to design, build and fly payloads or vehicle components that address research needs of different subsystems on the SLS. Teams will share the research results, which will be used in future design and development of SLS and other projects.
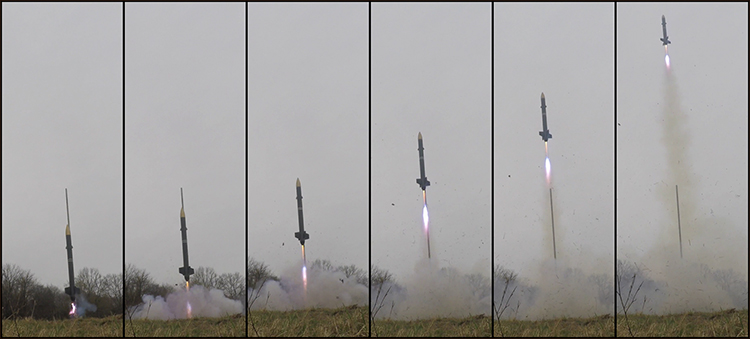
Contact: Brenda Ellis, (615) 343-6314
Brenda.Ellis@Vanderbilt.edu
Twitter @VUEngineering