Vanderbilt engineers used a drop of rubbing alcohol, an office laminator and creativity to develop scalable processes for manufacturing single atom thin membranes. Their membranes outperformed state-of-the-art commercial dialysis membranes and the approach is fully compatible with roll-to-roll manufacturing.
Details of the imaginative experiment are recently published in the journal of the Royal Chemistry Society: “Scalable Synthesis of Nanoporous Atomically Thin Graphene Membranes for Dialysis and Molecular Separations via Facile Isopropanol-Assisted Hot Lamination.”
Graphene membranes present potential for breakthrough advances in separation of a variety of microscopic ions and molecules, including salts, proteins or nanoparticles, and are relevant to industrial applications for water desalination and gas separations. Such membranes also are useful for chemical, biological and medical research and the purification of substances used in pharmaceuticals.
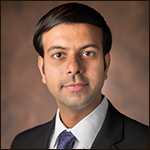
“As engineers we are always looking to make technologies scalable and this is an important step toward making graphene membranes scalable and practical for manufacturing,” said Piran R. Kidambi, assistant professor of chemical and biomolecular engineering. “Fabrication of roll-to-roll high-quality monolayer graphene is imperative to advance nanoporous atomically thin membranes (NATMs) for molecular separations.
“What’s challenging is the process of transferring the graphene to the supporting polymer layer to make functional membranes,” Kidambi said. “Polymer scaffolds commonly used for graphene transfer typically leave polymer residues and other contaminants that can affect the performance of single atom thick membranes, and transfers without polymer scaffolds suffer from low yield resulting in unwanted leakage.”
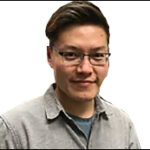
Kidambi and his lab team, first author Peifu Cheng and Nicole K. Moehring, in collaboration with scientists at Oak Ridge National Lab, Juan Carlos Idrobo and Ilia N. Ivanov, show that a hot lamination process using rubbing alcohol enables a clean transfer of graphene on to polycarbonate supports with 99.2% coverage while preserving support porosity.
“We demonstrate fully functional centimeter-scale graphene membranes that show record high permeances—orders of magnitude higher—and better selectivity than commercially
available state-of-the-art polymeric dialysis membranes,” Peifu said. “This is a scalable approach to fabricate graphene membranes for practical applications and is fully compatible with roll-to-roll manufacturing processes.”
This work is supported by an American Chemical Society PRF Grant #59267-DNI10, and an NSF CAREER award #1944134.
Contact: Brenda Ellis, 615 343-6314
brenda.ellis@vanderbilt.edu