A recent mechanical engineering doctoral graduate has created a material for welding in extreme conditions that could minimize equipment needed and operator hazards.
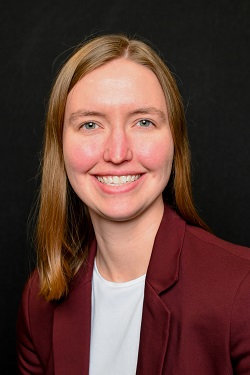
The material—a safe, stable, thermite paste—can serve as a portable, programmable heat source for use in space, under water and in combat zones. The paste is 3D-printed and deposited in patterns called reactive material architectures that can be controlled and directed.
“I think it has a lot of potential,” said Neely, Ph.D. ‘20. “You just print it, put it on the joint and light it.”
Neely, who starts her job as an aerospace engineer at NASA Marshall Space Flight Center in August, successfully used the printed paste to heat solder to fuse aluminum, and, more recently, copper lap joints.
The paste is about the consistency of peanut butter. The recipe starts with a well-mixed blend of iron oxide, aluminum powder and gypsum powder. Addition of water activates the gypsum powder as a binder; the paste begins to cure immediately. Addition of tartaric acid to the water before mixing can slow down curing, but even then, working time is limited to less than 45 minutes or paste becomes too thick and sticky to print, Neely said.
Her thermite paste is safe to create, print and transport.
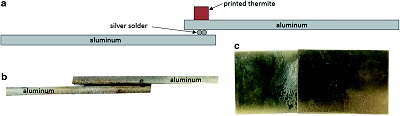
“If anything, I have an overdeveloped sense of safety,” Neely said.
Other researchers have developed printed reactive material that can be controlled at the nanoscale but only small amounts of it can be deposited, limiting how much energy can be used. At the macroscale, at least ½ millimeter, another approach uses fluoropolymer-based reactive materials but requires special techniques to synthesize the polymer and refine the filament so the material doesn’t ignite unintentionally.
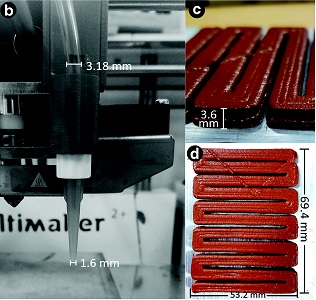
In her work Neely, who also received her BE in mechanical engineering at Vanderbilt, combined two interests—3D printing, or in this case, 4D printing—and energetic materials. The extra dimension is time; a 4D material transforms over time, reacting to an environmental stimulus such as humidity or temperature and changing form. She credits Alvin Strauss, professor of mechanical engineering, and Kevin Galloway, assistant professor of mechanical engineering and Vanderbilt’s director of making, her Ph.D. advisers, work, for green-lighting the idea.
Their study, “Soldered copper lap joints using reactive material architectures as a heat source,” was published in the April 2020 issue of Manufacturing Letters. “Additively Manufactured Reactive Material Architectures as a Programmable Heat Source,” which included foundational work, was published in August 2019 in 3D Printing and Additive Manufacturing. The work has been supported by The U.S. Naval Sea Systems Command NAVSEA through the Naval Engineering Education Consortium NEEC Grant #N00174- 19-1-0020 and the NASA Tennessee Space Grant Consortium.